<< назад : вперед >>
Схемы высадки головок
стержневых крепежных деталей
До
сих пор неизвестно, когда произошло появление на Земле винта – прототипа
современных резьбовых крепежных деталей. Винты, датированные многими веками
до Рождества Христова, археологи находят и в Китае, и в Азии, и на
американском континенте. Причем по точности изготовления древнейшие изделия
порой превосходят более поздние образцы…
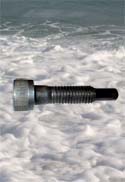
подробнее
>>
Вопросы технологии
маркировки резьбовых крепежных деталей
Уже
более 100 лет определить, кто производитель и какими механическими и
эксплуатационными свойствами обладает крепежная деталь, позволяет маркировка…
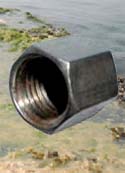
подробнее
>>
Разделительные операции в
технологии холодной объемной штамповки деталей
Технология
изготовления деталей холодной объемной штамповкой строится на основе
необходимого и достаточного количества…
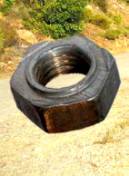
подробнее
>>
Проблемы
развития метизного производства для автомобильной промышленности России
Необходимость
повышения качества и технического уровня крепежных деталей и пружин для
обеспечения потребностей автомобильной промышленности сегодня ни у кого не вызывает сомнений.
На
автомобильных заводах понимают, что повышение конкурентоспособности
российских автомобилей и их качества, которого ждут все нынешние и
потенциальные автовладельцы, зависит (в том числе) от качества крепежа и
пружин…
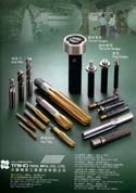
подробнее >>
Перспективы
внедрения прогрессивного крепежа в автомобильной промышленности России
В
настоящее время на сборочных линиях и в цехах Волжского автомобильного завода
используется крепеж, разработанный и изготовленный по нормативной
документации, переданной с технологией FIAT–ВАЗ в середине 60-х годов
прошлого столетия…
Прогрессивный
крепеж – источник снижения затрат на производство и эксплуатацию АТС
Покупая
автомобиль, обычно принимают во внимание соотношение его качества и цены, не
упуская из внимания системы безопасности, длительность пробега без
регулировок и ремонта, эксплуатационные расходы. При этом едва ли кого-нибудь
интересует, какие крепежные детали использованы в сборке автомобиля…
Технический контроль
качества автонормалей у производителя, дилера и потребителя
Основная
прибыль от продажи автомобильных и автомоторных крепежных деталей зависит от
объемов спроса, заявленной цены, рекламы, ассортимента и товарного качества
продукции…
Разделительные операции в
технологии холодной объемной штамповки деталей
Технология
изготовления деталей холодной объемной штамповкой строится на основе
необходимого и достаточного количества…
Из публикации
Сухов А. «ВИНТ и ГАЙКА: СПИРАЛЬ ЭВОЛЮЦИИ»
Все "зримые"
достижения техники, среди которых, безусловно, и автомобиль, были бы
невозможны без эволюции невзрачных железок - винтов, отверток, ключей. Более
того, инструмент и технологии, пожалуй, лучше всего иллюстрируют уровень
развития общества, ведь готовое изделие - лишь их производное, порой
скрывающее многие секреты изготовления. Вспомним столько веков…
Из публикации
Львова А. «СОЖ по спецзаказу»
Большинство
смазочно-охлаждающих технологических сред, применяемых в металлообработке,
представляют собой смазочно-охлаждающие жидкости (СОЖ). В 70-е годы, когда
80% всех СОЖ производилось на Украине, их номенклатура исчислялась единичными
марками, сейчас – сотнями…
Из публикации
Рикошинский А. «Склады промышленных предприятий»
Эффективность
функционирования промышленного предприятия зависит не только…
Автореферат
диссертации канд. техн. наук
Скворцовой С.С. «Совершенствование процессов формирования потребительских
свойств колесных болтов на основе оценки качества технологий»
Качество
продукции относится к числу важнейших показателей рейтинга и
конкурентоспособности предприятия как на внутреннем, так и на внешнем рынках.
Повышение качества изделий в значительной мере определяется темпами
научно-технического прогресса, техническим уровнем предприятия, способами и
методами организации производства…
Инструкция
по фосфатированию металла под холодную высадку
Настоящая технологическая инструкция предусматривает
технологию подготовки поверхности металла к высадке деталей на отечественных
и импортных холодновысадочных автоматах.
Технологический
процесс подготовки поверхности заключается в фосфатировании…
По рекламным
материалам: FOERSTER: 100% вихретоковый контроль прутков и проволоки
В
1937, исследуя магнитные свойства металлов, Фридрих Фёрстер обнаруживает
влияние магнитного поля земли на магнитную катушку контрольной установки. Он
начинает с разработки высоко чувствительных устройств измерения для магнитных
полей. В 1948 он создает свою собственную компанию и ищет способы использовать
результаты, которых он достиг в научной работе в Кайзер-Вильгельм Институте…
По
рекламным материалам: LOCKTITE:
Жидкие устройства для предотвращения самоотвинчивания и фиксации резьбы
Устройства
для предотвращения самоотвинчивания в автомобильной промышленности должны
соответствовать высочайшим стандартам в вопросах фиксации резьбы. Резьбовой
фиксатор создает соединение граничных резьбовых плоскостей, сцепляющее
шероховатости их поверхностей, для предотвращения любых перемещений резьбовых
деталей. Таким образом, проблема решается там, где она возникает, а именно в
резьбе…
Сталь для
холодной высадки
Концерн Oy Ovako Ab - крупнейший производитель стали и особенно стали
для холодной высадки в Европе. В качестве сырья на Коверхарском металлургическом
заводе, плавка стали в кислородном конвертере, используются низкофосфористые
железорудные окатыши и отборный металлолом. В сочетании с технологией
непрерывной разливки стали и обработкой стали в печи-ковше, такое сырье
позволяет обеспечить однородный химический состав, необходимую внутреннюю
структуру, а также отличное качество поверхности заготовок…
Опыт создания
производства шаровых пальцев для поставки ведущим мировым производителям
систем передней подвески рулевого управления
Закрытое акционерное
общество научно-производственное объединение «БелМаг» было основано 30
декабря 1996 года в металлургической столице России Магнитогорске,
расположенном у подножия Уральских гор на границе Европы и Азии. Стратегическая цель предприятия – выпуск
высококачественных автомобильных деталей и узлов…
Атлас
микроструктур сталей, применяемых в автомобилестроении. Тихонов А.К., Копыл
М.Д., Невзорова Н.В., Черданцев А.Н. ДИС АО «АвтоВАЗ», Тольятти, 1999. – 77
с.
|
Защитные цинковые покрытия
для крепёжных изделий
Агеев В.С., генеральный директор
Кабанов Е.Б., главный научный сотрудник
ООО «НПЦ мостов»
Ерофеев В.С., начальник технологического отдела
«Гипрометиз»
«Гипрометиз»
В последнее время для метизных предприятий всё
острее встаёт вопрос по увеличению срока службы выпускаемых крепёжных
изделий. Одним из наиболее эффективных способов достижения этой цели является
нанесение защитного цинкового покрытия. Обладая стационарным потенциалом на
0,2-0,3 мВ более отрицательным, чем железо, цинк при воздействии агрессивных
сред (в виде электролитов) медленно растворяется за счёт электрохимических
реакций при постоянном обновлении защитных пассивных плёнок, защищая, тем
самым, ферритную подложку. Таким образом, цинковое покрытие выполняет роль
протектора, «размазанного» по поверхности защищаемого изделия. За последние
несколько десятилетий цинковое покрытие продемонстрировало высокие
потребительские качества, позволяющие использовать его практически во всех
сферах промышленности. Срок службы оцинкованного крепежа даже в
промышленно-приморской атмосфере может достигать 30 лет, а увеличение
жизненного цикла соединений помогает сократить затраты на ремонт и
обслуживание. В зависимости от назначения и характеристик крепежа используют
различные способы нанесения покрытий, каждый из которых имеет свои
преимущества и недостатки.
Сегодня у метизных предприятий существует широкий выбор
технологий цинкования продукции. Наряду с давно зарекомендовавшей себя
технологией гальванического цинкования существует ряд новых методов нанесения
цинкового покрытия, таких как термодиффузионное, цинкламельное и механическое
цинкование крепёжных изделий. В этой статье мы постараемся описать
технологии, применяемые на территории СНГ, и дать им объективную оценку.
Технология цинкования является одним из наиболее
распространённых в промышленности методов защиты крепежа от коррозии. Высокие
защитные (антикоррозионные) свойства этого покрытия объясняются тем, что в
наиболее часто встречающихся коррозионно-активных средах (в промышленной и
морской атмосфере, в пресной минерализированной и в морской воде) цинк
является анодом почти ко всем применяемым металлам (кроме алюминия и магния).
Благодаря этому, цинк растворяется в этих средах, а сталь (как катод) не
подвергается разрушению до тех пор, пока на ней есть слой цинка.
Основным показателем цинкового покрытия является его коррозионная стойкость,
выражаемая в виде срока службы в годах. Для ускоренной оценки защитной способности
металлизационных, в частности и цинковых покрытий, применяют ускоренные
климатические испытания до появления первых признаков коррозии, по
результатам которых полученная долговечность с помощью коэффициентов
ускорения (обычно Куск.=17-20) оценивается прогнозируемый срок
службы покрытия. Для крепёжных изделий, требующих декоративных качеств
покрытия, признаком начала коррозии служит показатель сохранности покрытия на
5-10 % площади покрытия. Для общепромышленного крепежа таким показателем
является сохранность его на 50 % покрытой площади.
На сегодняшний день существует пять основных технологий нанесения цинкового
покрытия на крепёжные изделия, а именно: гальваническое, термодиффузионное,
горячее, механическое и цинкламельное цинкование. Самой распространённой на
сегодняшний день является технология гальванического цинкования, с описания
которой мы и начнём обзор.
Технология гальванического
цинкования
Технология электролитического цинкования представляет собой химический
процесс электролиза и заключается в следующем: в ванну с электролитом
погружаются два металла, в данном случае стальные цинкуемые детали и цинковые
пластины, которые подключаются к полюсам источника постоянного тока. В
процессе электролиза цинковая пластина (анод) растворяется, и его ионы
оседают на поверхности стального крепежа, формируя гальваническое покрытие,
толщиной от 5 до 25 мкм. Анодное растворение цинковых электродов происходит в
результате пропускания через электролит электрического тока с катодной
плотностью от 1 до 5 А/дм2.
При этом методе цинкования получают точного размера равномерные, блестящие,
декоративного вида покрытия, отличающиеся, к сожалению, низкими адгезионными
свойствами. Адгезия гальванических покрытий обеспечивается молекулярными
силами, действующими между молекулами цинка и основного металла. Поскольку
сила такого взаимодействия резко убывает уже на расстоянии 30-50 ангстрем,
любые плёнки на поверхности покрываемых изделий в виде жировых или оксидных
составляющих, чего трудно избежать при массовом производстве, существенно
ухудшают качество покрытий.
В гальваническом производстве, в зависимости от назначения крепежа,
используют различные электролиты, которые делятся на три вида: цианидные,
щелочное и кислотные.
Цианидные ванны являются самыми высокотоксичными, из-за наличия в их составе
цианида натрия, а также едкого натра и оксида цинка. Изменяя процентное
соотношение составляющих, можно придавать различные свойства электролиту.
Положительными сторонами цианидных ванн являются: высокая производительность;
хорошая кроющая способность, позволяющая обрабатывать детали сложной формы;
долговечность электролита и лёгкость его обслуживания.
К недостаткам можно отнести высокую степень загрязнения окружающей среды
отходами производства и приобретаемую цинкуемой сталью водородную хрупкость,
которая является самым ощутимым минусом особенно для высокопрочного крепежа,
прошедшего через цианидные или кислотные ванны. Водородная хрупкость
значительно снижает статическую и усталостную прочность высокопрочных марок
стали.
Альтернативой цианидному электролиту могут стать щёлочные электролиты,
которые содержат 1-2 г оксида цинка и 10-20 г едкого натра на 1 л раствора.
Такие электролиты менее опасны для окружающей среды, чем цианидные ванны, но
и они не лишены существенных недостатков. Щелочные электролиты рекомендуется
применять только для обработки стали; процесс цинкования приостанавливается
при нагреве электролита выше +30оС; имеет место наводораживание
обрабатываемых деталей, что также способствует охрупчиванию стали;
оцинкованный крепёж имеет непривлекательный вид.
Наиболее перспективно гальваническое цинкование в слабокислых электролита,
способствующих хорошей укрываемости и улучшению внешнего вида цинкового
покрытия. Этот метод, кроме того, снижает склонность цинкуемой стали к водородной
хрупкости и позволяет цинковать детали сложной конфигурации, изготовленные
как из стали, так и из чугуна и цинко-алюминиево-медных сплавов. Институтом
Химии Литвы усовершенствована технология цинкования в слабокислых
электролитах, которая позволяет получать крепёжные изделия с цинковыми
покрытиями различных цветов и высокими декоративными свойствами.
Все гальванические технологии требуют высокого качества подготовки
поверхности обрабатываемых изделий. Непосредственно перед процессом
цинкования необходимо проводить очистку стали от оксидов (окалины) и
продуктов коррозии (ржавчины). После нанесения покрытия для большей
стабильности и стойкости его подвергают осветлению (активации поверхности
покрытия азотной кислотой) и пассивации (так называемое хроматирование –
создание дополнительного пассивного защитного слоя на поверхности самого
защитного покрытия). Пассивация может быть радужной (жёлтой), бесцветной
(белой или голубой) и чёрной.
При пассивации на большинстве предприятий применяют шестивалентный хром –
канцероген и яд. Главные недостатки таких покрытий – потеря коррозионной
стойкости при нагреве свыше 100°С и экологическая неприемлемость технологий.
С начала 2007 года вышел запрет на использование шестивалентного хрома в
пассивационных плёнках в автомобильной промышленности.
Замена хроматных плёнок на хромитные, не содержащие шестивалентный хром,
решает обозначенные проблемы. Пассивации с трёхвалентным хромом уже
применяются некоторыми производителями автомобильного крепежа, в таком
варианте покрытия удовлетворяют действующие нормы по коррозионной стойкости,
но оцениваются специалистами как неперспективные. Применение пассивирующих
растворов и электролитов, содержащих кислоты, цианиды и другие химически
активные соединения, заставляет организовывать в гальванических производствах
методы нейтрализации и глубокой очистки экологически опасных отходов, строить
дорогостоящие очистные сооружения, что, в конечном счете, нивелирует
положительные качества высокопроизводительных процессов нанесения гальванических
покрытий.
На сегодняшний день метод гальванического цинкования
является самым распространённым на предприятиях, производящих цинкование
крепежа. Это, в большей степени, обусловлено высокой производительностью
устоявшейся технологии производства и высоким спросом потребителей на данный
вид цинкования. Современные гальванические ванны позволяют наносить покрытия
на крепёжные изделия, не нарушая резьбу, с высокими декоративными свойствами,
что немаловажно для сегодняшнего потребителя. Наравне с этим существует
множество отрицательных сторон у данной технологии, таких как: высокая
износостойкость гальванопокрытий, экологический фактор и водородное
охрупчивание крепежа, что в ряде случаев делает электролитический метод
малоэффективным и даже неприемлемым (при обработке высокопрочного крепежа).
Технология горячего цинкования
Процесс нанесения цинкового покрытия «горячим» способом состоит из нескольких
этапов: первоначально детали обезжиривают, промывают, протравливают в кислоте
и повторно промывают. Далее детали помещают в барабан и окунают в ванну
(керамическую или чаще стальную) с расплавленным цинком, разогретым до
температуры приблизительно 465оС. Вращением барабана обеспечивают
проток цинковой массы относительно цинкуемых деталей для заполнения всех пор
и микрополостей. Затем барабан вынимают из ванны и раскручивают на центрифуге
для удаления излишков цинка. Метод позволяет удалить лишний цинк только с
наружной поверхности деталей, но на внутренней резьбе (на гайках) он не
эффективен, поэтому резьбу приходится протачивать повторно. Отсутствие
покрытия на внутренней резьбе безусловно влияет на коррозионную стойкость
соединения, однако, если гайка без покрытия применяется с горячеоцинкованной
ответной деталью (болтом или шпилькой), цинк при наличии коррозионно-активного
электролита будет в некоторой степени защищать непокрытую цинком поверхность
ответной детали при условии, что расстояние от цинкового покрытия до стальной
детали не превышает 2 мм. Это происходит за счёт высокой анодности цинка по
отношению к железу. В случаях применения горячеоцинкованного болта с
электролитически оцинкованной гайкой гальванический цинк, благодаря его
высокой пористости, будет интенсивно разрушаться.
Главным преимуществом технологии горячего цинкования является высокая
коррозионная стойкость, которая в несколько раз превышает стойкость
электролитически оцинкованного крепежа. Это позволяет применять
горячеоцинкованный крепёж в конструкциях высоковольтных столбов, башен и мачт
приёмопередатчиков мобильной связи и дорожных ограждений. К положительным
сторонам можно также отнести протектирующие свойства горячецинкового покрытия
для участков стальных изделий с повреждённым покрытием, а также высокую
прочность горячеоцинкованного крепежа класса прочности 8.8.
Не смотря на высокие показатели антикоррозионной стойкости горячецинкованного
покрытия и ряд других положительных сторон, данная технология не получила
широкого распространения для крепёжных изделий из-за высокой стоимости
нанесения покрытия, которая на 20-40% дороже электролитического цинкования.
Высокая стоимость горячего цинкования мелких изделий в виде метизов
определяется необходимостью поддержания требуемой температуры расплава цинка
путём его постоянного подогрева, даже в периоды, когда цинкование не
производится. Объёмы цинкования крепежа данным способом также сдерживаются
из-за необходимости проведения специальной предварительной механической
обработки крепежа (следует «обнизить» резьбу, оставив припуски для слоя
покрытия) и неравномерности нанесения цинка (при толщинах покрытия 40-60 мкм
наплывы цинка могут достигать 1 мм). Поэтому этот метод не применяется для
изделий диаметром менее 8 мм, поскольку цинк «забивает» мелкую резьбу. По
этим причинам в автомобильной и машиностроительной промышленности
горячеоцинкованные метизы не применяются. Декоративные характеристики
горячеоцинкованного крепежа также низки из-за глухого, серо-матового цвета
покрытия.
Таким образом, технология горячего цинкования более
приемлема для цинкования проволоки, гвоздей и других метизных изделий и не
пригодна для обработки крепежа из-за большой неточности нанесения покрытия и
высокой цены.
Технология термодиффузионного
цинкования
Отмеченные выше негативные
стороны вышеперечисленных способов цинкования заставили научно-техническую
общественность обратить более пристальное внимание на термодиффузионное
цинкование. К достоинствам этого метода можно отнести следующее:
детали цинкуются в
герметически закрытых ретортах, поэтому процесс диффузионного цинкования
экологически безопасен и не требует создания очистных сооружений;
получаемое покрытие не имеет
пор и за счёт диффузионного слоя имеет прочную адгезионную связь с подложкой;
процесс термодиффузионного
цинкования осуществляется при температурах от 380 до 4500оС, что
исключает термическую хрупкость и снижение механических свойств высокопрочных
сталей, из которых изготовляются крепёжные изделия, в результате
низкотемпературного отпуска;
защитная способность покрытия
многократно выше, чем у гальванических и горячецинковых покрытий и при
толщинах диффузионного покрытия около 50 мкм может достигать в условиях
эксплуатации в промышленно-приморской атмосфере не менее 15 лет;
толщина покрытия может быть
любой и зависит от времени выдержки цинкуемых деталей в печи;
диффузионный цинк покрывает
детали равномерным слоем без наплывов, точно повторяя профиль цинкуемой
поверхности, включая глухие отверстия, элементы сложной конфигурации, щели,
полости, резьбу и т.п.;
поскольку термодиффузионное
цинкование не требует подготовки поверхности метизов путём химического
кислотного травления, исключается наводораживание металла, что весьма опасно
для высокопрочных крепёжных изделий;
отходы производства не
требуют захоронения и могут быть использованы в качестве наполнителей
строительных бетонных смесей.
Среди недостатков метода
следует отметить:
отсутствие декоративных
свойств у диффузионного цинкового покрытия (глухие тона, отсутствие блеска),
но для метизов промышленного назначения декоративный вид не имеет большого
значения;
относительно небольшую
производительность, лимитируемую объёмами камер для цинкования; однако, уже
имеются установки термодиффузионного цинкования с ретортами, которые вмещают
до 1 т метизов за одну закладку, что свидетельствует о достаточной
производительности;
наличие вредных для здоровья
человека аэрозолей цинковой пыли; однако, поскольку термодиффузионное
цинкование осуществляется в герметично закрытых ретортах и имеются
специальные устройства для беспылевой загрузки-выгрузки порошкообразной
шихты, опасность от наличия вредных аэрозолей сведена до миниума. Способ
основан на технологии химико-термического насыщения цинком поверхности
изделий из порошковой смеси (метод «Шерардайзинга»).
Формирование покрытия осуществляется при контактном взаимодействии частиц
порошка цинкового сплава с очищенной и подготовленной поверхностью металла
основы, а также при взаимодействии железа с паровой фазой цинка, образующейся
при высокой температуре. За счёт диффузии цинка и легирующих элементов в
железе происходит образование интерметаллидных соединений цинка, легирующих
элементов и железа, являющихся основой защитного покрытия. При этом
образуется покрытие, равномерное по толщине на всех участках стального
изделия, включая резьбу, маркировку, щели и глухие отверстия за счёт
проникновения туда паровой фазы цинка.
Поверхностная диффузия цинка при формировании покрытия способствует
«заживлению» поверхностных дефектов крепёжных изделий, которые могли явиться
концентраторами напряжений, способствующих разрушению высокопрочного крепежа.
Для протекания диффузии необходимо создать условия для сближения разнородных
атомов металлов до расстояний, при которых возможно проникновение атомов
цинка и железа в структурную решетку соседнего металла. Для этого производят
тщательную очистку поверхности цинкуемого металла основы, вводят в
диффузионную смесь флюсующие активаторы, герметизируют контейнер и пытаются
внутри него создать инертную или восстановительную атмосферу.
Процесс осуществляется в диапазоне температур от 370 до 600°С. Повышенные
температуры способствует ускорению диффузии, но формируемые при этом покрытия
очень хрупки и могут отслаиваться, а формируемые при этом на поверхности
стального изделия интерметаллические соединения железа и цинка не отличаются
высокой коррозионной стойкостью. Формирование покрытия наиболее оптимально
при низких температурах (около 420°С).
Одним из наиболее весомых плюсов данной технологии является высокая
коррозионная стойкость покрытия. Адгезия диффузионных покрытий очень высока,
поскольку цинк за счёт диффузии проникает в основной металл примерно на 1/3
толщины покрытия.
Термодиффузионное покрытие характеризуется высокой точностью соблюдения
заданной толщины (± 20 %), которая может составлять от 25 до 110 мкм. В связи
с этим данный метод можно применять для защиты от коррозии мелких изделий
(например, шайбы) и изделий с резьбой, (например, гайки, мелкие винты, шурупы
и т.д.), эксплуатируемые в условиях повышенной агрессивности сред. Следует
отметить, что данная технология цинкования полностью исключает водородное и
коррозионное охрупчивание высокопрочных болтов. Термодиффузионное покрытие
обладает высокой износоустойчивостью и термостойкостью.
В отличие от гальванической технологии термодиффузионный метод не имеет
вредных отходов и позволяет экономить производственные площади,
электроэнергию и рабочую силу, что в итоге сказывается на снижении
себестоимости самого процесса.
Однако, при таком большом перечне преимуществ данный метод имеет и некоторые
недостатки – это отсутствие декоративных свойств внешнего вида покрытия,
который имеет серую матовую окраску. Но в последнее время уже разрабатываются
и внедряются пассивирующие и блескообразующие составы, улучшающие внешний вид
обработанных изделий.
Крепёжные изделия с термодиффузионным покрытием могут быть
использованы для соединения крупных, металлоёмких строительных конструкций и
сооружений, а также для элементов с алюминиевым или цинковым покрытием, в
автомобильной, автотракторной промышленности, машиностроении, станкостроении,
а также в любых других отраслях, где существует необходимость применения
высокопрочного крепежа с повышенными антикоррозионными показателями при
условии, что декоративные свойства имеют второстепенный характер.
Механический метод цинкования
Формирование цинкового покрытия механическим методом происходит следующим
образом: деталь вместе со стеклянными шариками и цинковой суспензией в водном
растворе загружаются во вращающийся галтовочный барабан или колокол. Шарики
выполняют роль элемента, «втирающего» в сталь покрытие за счёт взаимодействия
деталей с суспензией при вращении барабана. Механическим втиранием можно
получать тонкие (8-10 мкм) и толстые (15-20 мкм) цинковые покрытия с
невысокой точностью нанесения. Вся операция происходит при комнатной
температуре, что позволяет значительно экономить электроэнергию.
Немаловажной особенностью механического цинкования, как и у
термодиффузионного метода, является отсутствие появления водородного
охрупчивания деталей. Вследствие применения чистого цинка покрытие имеет
высокие декоративные свойства, что позволяет применять крепёж с таким
покрытием в мебельном производстве и при отделке жилых помещений.
Долговечность данного покрытия сопоставима с гальваническим и составляет
приблизительно 1-2 года.
Необходимо отметить, что механический способ не обеспечивает высокую степень
сцепления цинкового покрытия с основным металлом изделия, что делает
неприемлемым его применение в ответственных отраслях.
Главное направление данной технологии – декоративная отделка
жилых помещений и предметов быта, не находящихся под воздействием агрессивных
сред. Небольшие габариты установки для механического цинкования и низкие
затраты на сам процесс – вот главные преимущества данной технологии. Этот
метод удобно использовать для цинкования крепёжных деталей в небольших цехах,
с малыми объёмами производства, где применение «традиционной» гальваники
проблематично.
Технология цинкламельного покрытия
В данной технологии нанесение покрытия проводится специальными растворами, состоящими
из 80% цинка с добавлением алюминия и связующих элементов. Цинковое покрытие
может наноситься несколькими способами: спрей-статиком, окунанием корзины с
деталями в раствор, а также с помощью галтовочных барабанов и колоколов.
Покрытие не содержит соединений шестивалентного хрома и других экологически
вредных тяжёлых металлов.
Цинкламельное покрытие состоит из базового слоя и, при необходимости, одного
или нескольких дополнительных слоев, придающих покрытию специальные свойства:
фрикционные, декоративные, пластичные, стойкость к тепловым и механическим
нагрузкам, химическую стойкость по отношению к агрессивным жидкостям. Базовый
слой состоит из цинковых и других металлических чешуек, расположенных
параллельно друг другу и поверхности детали, толщиной несколько десятых
микрона, соединённых электропроводящим связующим компонентом.
В зависимости от требований по коррозионной стойкости толщина покрытия может
составлять от 4 до 100 и более мкм. Для цинкламельного покрытия характерна
высокая коррозионная стойкость, которая составляет более 700 часов в соляном
тумане (5-7 лет) при толщине покрытия 9-10 мкм. Покрытие отличает высокая
термостойкость – детали сохраняют работоспособность более 2000 часов при
температуре свыше 2000°С. В процессе нанесения покрытия отсутствует выделение
водорода и, соответственно, наводораживание обрабатываемых деталей.
Пластичность нанесённого покрытия обеспечивает на крепёжных изделиях
сохранность резьбы и маркировок. Отличительной особенностью данной технологии
является широкий выбор цветовой гаммы покрытий, что позволяет использовать
крепёж в декоративных целях.
Прочность покрытия, нанесённого данным способом, ниже прочности покрытия,
нанесённого гальваническим способом, и зависит от требований, выдвигаемых к
детали и её геометрии. Изменяя способ нанесения, можно изменять его свойства,
это также относится и к износостойкости. Прочность покрытия напрямую зависит
от декоративных свойств, т.е. если деталь будет использоваться как видовая,
его прочностные характеристики будут ниже, чем у подобной с худшими
декоративными свойствами.
Технология цинкламельного нанесения покрытий в последнее
время получила широкое распространение в автомобильной промышленности. Это
обусловлено высокими антикоррозионными свойствами при небольшой толщине покрытия
и широким выбором его цветов. Данная технология по затратам находится в одном
ценовом диапазоне с классической гальваникой, но при этом с лучшим
показателем коррозионной стойкости. Отрицательным фактором является низкая
износостойкость покрытия (повреждения при ударах) и неспособность выполнять
протектирующие свойства на повреждённых участках.
Вывод
Каждая из вышеперечисленных технологий имеет свои положительные и
отрицательные стороны, и не существует однозначного ответа на вопрос, как
лучше оцинковывать крепеж. Выбор технологии цинкования зависит от требований,
выдвигаемых к крепежу, и от условий его эксплуатации.
Источник информации: Журнал
«Крепеж, клеи, инструмент и….» №3(21) 2007
|
Бернштейн
М.Л. Структура Деформированных металлов. – М.: Металлургия, 1977. – 431 с.
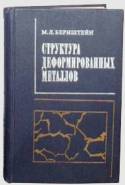
Содержание
книги >>
Главы из
книги И. Биллигман «ВЫСАДКА И ДРУГИЕ МЕТОДЫ ОБЪЕМНОЙ ШТАМПОВКИ»
Значение инструмента
весьма возросло в связи с развитием методов штамповки, развитием
пресс-автоматов, а также в связи с расширением области применения штамповки.
Высокую производительность…
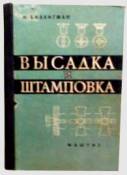
Содержание
книги >>
Главы из
книги Петриков В.Г., Власов А.П. «ПРОГРЕССИВНЫЕ КРЕПЕЖНЫЕ ИЗДЕЛИЯ»
Накатывание резьбы предоставляет
широкие возможности для изменения и создания благоприятной структуры металла
стержня и качества поверхности резьбы, так как позволяет формировать…
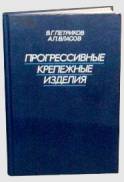
Содержание
книги >>
Главы из
монографии Губкин С.И. «ПЛАСТИЧЕСКАЯ ДЕФОРМАЦИЯ МЕТАЛЛОВ»
ГЛАВА 1. Часть 4. Упрочнение (Наклеп)
Интенсивность увеличения сопротивления деформированию с
увеличением степени деформации отображает эффект наклепа. Интенсивность
наклепа зависит от особенностей пластического процесса при данных условиях
деформации…
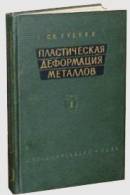
подробнее
>>
Губкин
С.И. Пластическая деформация металлов. Том II. Физико-химическая теория пластичности. - М.:
Металлургиздат, 1961. – 416 с.
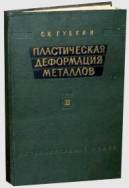
подробнее
>>
Губкин
С.И. Пластическая деформация металлов. Том III. Теория пластической обработки металлов. - М.:
Металлургиздат, 1961. – 306 с.
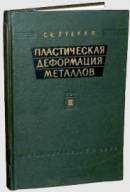
подробнее
>>
Ковка и
штамповка: Справочник. В 4-х т./Ред. совет: Е.И. Семенов (пред.) и др. – М.:
Машиностроение, 1985 – т. 1. Материалы и нагрев. Оборудование. Ковка / Под
ред. Е.И. Семенова. 1985. – 568 с.: ил.
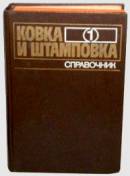
Содержание
книги >>
Ковка и
штамповка: Справочник. В 4-х т./Ред. совет: Е.И. Семенов (пред.) и др. – М.:
Машиностроение, 1986 – т. 2. Горячая штамповка / Под ред. Е.И. Семенова.
1986. – 592 с.: ил.
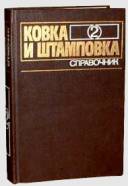
подробнее
>>
Ковка и
штамповка: Справочник. В 4-х т./Ред. совет: Е.И. Семенов (пред.) и др. – М.:
Машиностроение, 1987 – т. 3. Холодная объемная штамповка / Под ред. Г.А.
Навроцкого. 1987. – 384 с.: ил.
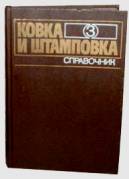
Содержание
книги >>
Ковка и
штамповка: Справочник. В 4-х т./Ред. совет: Е.И. Семенов (пред.) и др. – М.:
Машиностроение, 1985 - 1987 – т. 4. Листовая штамповка / Под ред. А.Д. Матвеева.
1985 - 1987. – 544 с.: ил.
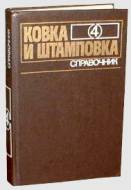
подробнее
>>
Главы из книги
Ч. Уик «ОБРАБОТКА МЕТАЛЛОВ БЕЗ СНЯТИЯ СТРУЖКИ»
Выражение «обработка
металла без снятия стружки» все чаще служит общим названием новых методов
холодного деформирования металла для получения готовых изделий…
Основные свойства
металла, применяемого для высокоэффективной и качественной высадки деталей в
отечественной и зарубежной практике.
Изготовление крепежных изделий
методом холодной высадки и выдавливания в различных отраслях промышленности
из года в год заметно увеличивается…
Перспективы
внедрения прогрессивных конструкций крепежных деталей и технологии их
изготовления в автомобильной промышленности
Одним из направлений
технического прогресса в автомобильной промышленности, в значительной степени
определяющей уровень производительности труда…
Современные
способы термообработки, обеспечивающие получение структуры стали, необходимой
для холодной высадки
Углеродистые и легированные
стали, применяемые для холодной высадки, относятся к феррито-перлитному
классу. При поставке подкат обычно имеет структуру: феррит + пластинчатый
перлит. При такой структуре заполняемость полостей матрицы и пуансона
ухудшена из-за низкой штампуемости стали. Лучшей пластичностью обладает…
Из публикации
Полозов Ю.А., Грушовенко А.Е. «Маркировка в автопроме: время диктует свои
законы»
Традиционное
маркирование используется в современных производствах с разными целями. Так, личные
клейма рабочих указывают на исполнителя детали, штампами ОТК отмечают годные
изделия, прошедшие испытания…
Из публикации
Фредерик Е. Грейвс «БОЛТЫ и ГАЙКИ»
Способ механического соединения,
представляющий собой комбинацию двух элементов - болта и гайки, имеет, как
нам кажется, древнее происхождение и достиг на сегодняшний день полного
совершенства. В действительности же болты и гайки с винтовой нарезкой
появились лишь где-то в середине XV в…
Из публикации
Сухов А. «ВИНТ и ГАЙКА: СПИРАЛЬ ЭВОЛЮЦИИ»
Все "зримые"
достижения техники, среди которых, безусловно, и автомобиль, были бы невозможны
без эволюции невзрачных железок - винтов, отверток, ключей. Более того,
инструмент и технологии, пожалуй, лучше всего иллюстрируют уровень развития
общества, ведь готовое изделие - лишь их производное, порой скрывающее многие
секреты изготовления. Вспомним столько веков…
Из публикации
Львова А. «СОЖ по спецзаказу»
Большинство
смазочно-охлаждающих технологических сред, применяемых в металлообработке,
представляют собой смазочно-охлаждающие жидкости (СОЖ). В 70-е годы, когда
80% всех СОЖ производилось на Украине, их номенклатура исчислялась единичными
марками, сейчас – сотнями…
Из публикации
Рикошинский А. «Склады промышленных предприятий»
Эффективность
функционирования промышленного предприятия зависит не только…
Миропольский
Ю.А., Мансуров И.З. Современные тенденции развития технологии холодной
объемной штамповки. М.: НИИмаш, 1979. – 80 с.
РТМ 37.002.0208-81.
Объемная штамповка крепежных деталей. Конструктивные и технологические
расчеты. - Горький, 1983. – 249 с.
|